PRODUCT
صفحة رئيسية>منتجات>
iron ore size after crushing at steel mill
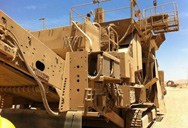
Crushing characteristics and performance evaluation of iron ore in
2023年12月1日 Iron ore: Cone crusher: Density, ρ (kgm −3) 4156.4: 7800: Shear modulus, E (Nm −2) 1.241e + 11: 7e + 10: Poisson's ratio, υ (–) 0.3: 0.3: Sub-particle radius, R (mm) 2.02605–7.97219: Meta-particle diameter, D (mm) 55: Meta-particle This step involves breaking up the iron ore to obtain an F 80 grind size before it can be ground. Once the ore has been crushed, it is diverted to a stockpile. The aim of this step The six main steps of iron ore processing - Multotec2022年1月1日 Abstract. Hematite and magnetite, the two predominant iron ores, require different processing routes. High-grade hematite direct shipping ores generally only Comminution and classification technologies of iron ore
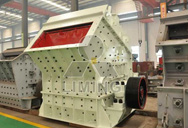
Iron Ore Processing: From Extraction to Manufacturing
2024年4月26日 Crushing is the initial stage in the iron ore processing journey, where large chunks of ore are broken down into smaller fragments. The primary objective of crushing Making iron and steel from iron ore requires a long process of mining, crushing, separating, concentrating, mixing, agglomeration (sintering and pelletizing), and shipping Iron Ore Processing, General2022年10月20日 Making iron and steel from iron ore requires a long process of mining, crushing, separating, concentrating, mixing, agglomeration (sintering and pelletizing), Iron Ore Processing, General SpringerLink
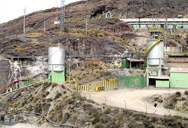
Comminution features in an impact hammer mill - ScienceDirect
2013年2月1日 Rosin–Rammler plot of the size distribution for Expt. no. 1 for crushing iron ore and coal in the impact hammer mill. The median size (d 50 ) of each product The most commonly used type is Iron Ore Fines (generally known as Sinter Feed) which is sin- tered at the receiving steel mill, prior to being charged to the blast furnace. Iron Ore Briefing: Relevance of Iron Ore to OBMsThe purpose of the primary crusher is to reduce the ROM ore to a size amenable for feeding the secondary crusher or the SAG mill grinding circuit. The ratio of reduction through a primary crusher can be up to AMIT 135: Lesson 5 Crushing – Mining Mill Operator
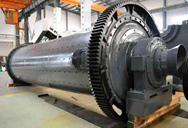
(PDF) Grinding Media in Ball Mills-A Review
2023年4月23日 The energy con sumption for spherical balls was 3.6 Kw after grinding for 420 minutes, producing a 45µm. residue of 4.37% whilst that of cylpebs was 2.6kW after grinding for 295 minutes producin ...
- rotary kiln for iron ore
- معدات معالجة المعادن مطحنة الكرة الخام
- آلة كسارة صغيرة في العراق
- خطط محطم خام المحمولة
- آلة محطم الرماد المطلوبة الفك
- الكرة مطحنة التكنولوجيا آلة طاحونة
- محمول الذهب الخام المورد كسارة الفك في أنغولا
- هزینه معدنی آسیاب توپ استفاده می شود
- تولید کنندگان داخلی از آسیاب غلتکی
- شراء المطاحن في الصين
- نوع من كسارة الحجر آلة كسارة الحجر الصين
- كسارة الفك مطحنة ريموند كسارة الفك
- مخلوط ماسه از پشت شکستن
- كسارة آسيوية كسارات تجوس
- الذهب معدات التعدين الاهتزاز آلة تهتز المغذية
- به طور خاص طراحی کمپرسور
- شركة التعدين في دبي
- الهند معدات معالجة خام الذهب
- آلة تكسير الحجر باليونان 185 tph
- تولید کنندگان ماشین آلات سنگ شکن آمریکایی